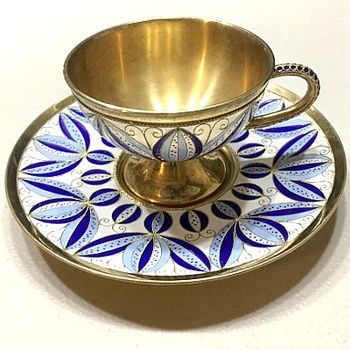
Искусство художественной эмали насчитывает более двух тысяч лет.
Древнейшими из известных изделий с использованием эмали являются металлические предметы с впаянными пластинками синего стекла, изготовленные между 1425 и 1300 гг. до н. э., которые были найденные в Микенах (Греция). С VI в. до н. э. греки систематически наплавляли эмаль на золотые украшения. Значительный вклад в технологию внесли Иран (Персия), Индия и Китай. Классическая история искусства рассматривает развитие художественного эмалирования в связи с формированием культуры центрально - европейских стран.
Эталонными образцами, оказавшими решающее влияние на ювелирное искусство средневековой Европы, считаются перегородчатые византийские эмали по золоту, созданные до XII в. Основным технологическим принципом эмалирования является обжиг металла и цветной стекловидной массы (эмали), при котором происходит прочное соединение, сцепление материалов друг с другом при высокой температуре. Традиционными приемами художественного эмалирования являются перегородчатые эмали, выемчатые, эмали по чеканному рельефу, витражная эмаль, живописная эмаль, миниатюра на эмали, эмаль по гильошированному фону.
Украшения с эмалью пришли к нам из глубокой истории. Этими технологиями обладали еще древние египтяне и римляне, которые создавали великолепнейшие предметы своей культуры и редчайшие по красоте ювелирные аксессуары.
В Древней Руси техника работы с эмалью была известна еще в Х веке. Однако наши предки называли ее “финифтью”, что с греческого означает “блестящий”. Помимо ювелирки и домашней утвари часто это покрытие использовали для украшения церквей, дворцов и домов зажиточных людей, а также для создания икон.
А в прошлом веке родился стиль модерн, который очень сильно отразился на росте популярности этой технологии. Плюс развитие химии позволило значительно расширить цветовую палитру эмали, что позволило ювелирам создавать непревзойденные по своей красоте украшения.
Несмотря на значительную и убедительную историю, художественное эмалирование все еще находится в процессе развития, и качество работы определяет в первую очередь практический опыт эмальера, так как сложные проблемы состава эмалей, обжига и сцепления металла с эмалью, а также многие другие технические вопросы продолжают совершенствоваться.
Художники, работающие сегодня с традиционными ювелирными эмалями, также активно используют и горячие технические эмали, что позволяет им расширить художественную выразительность современных образов и форм. Произведения российских художников – эмальеров по достоинству оценены не только на отечественных профессиональных художественных выставках, но и на крупнейших международных форумах: в старинном эмальерном центре Европы – Лиможе (Франция), в Ла Корунье (Испания), Ковингтоне (США) и других городах и странах мира.
Горячая эмаль: ее виды и технология и нюансы изготовления
Технология нанесения горячей эмали на ювелирные украшения намного сложнее чем холодной:
Сырье для создание эмали представляет собой стекловидные пластины, которые мастер размельчает до получения порошка и перемешивает с водой, делая пасту.
Непрозрачная эмаль получила «прозвище» – «глухое покрытие».
Затем украшение отправляется в печь для застывания. Температура выбирается в зависимости от того, из какого сплава сделано украшение и какой состав эмали применяется.
После обжига изделие шлифуется и повторно отправляется в печь для получения идеально красивой и гладкой поверхности эмали.
Нанесение эмали на ювелирные изделия – технологически очень сложная процедура и зависит от того, насколько затейливый рисунок предстоит сделать на украшении. Мастера говорят, что запекать изделие ювелир может до 100 раз, а главное при этом – точно выдержать технологическую процедуру, в обратном случае изделие можно легко испортить.
Существует несколько разновидностей горячей эмали: • перегородчатая. В этом случае паста заливается в ячейки или так называемые ленточки между перегородками в украшении, которые напаиваются на изделие заранее. Эксперты говорят, что такая техника создания красоты пришла к нам из Византии; • выемчатая. Эмаль заливается в выемки украшения, которые высверливаются и выпиливаются в изделии по форме рисунка. В этой технике главное – правильно и аккуратно создать выемки на крохотном аксессуаре.
Роспись цветной эмалью
Также существует интересная технология росписи посуды и предметов быта цветной холодной эмалью. Конечно, тут не используются никакие перегородки и выемки. Материал наносят слоями специальным инструментом и поэтапно обжигают изделие до тех пор, пока художник не закончит запланированный дизайнером эскиз.
А еще очень интересна технология сеянной холодной эмали, когда роспись рисунка выполняется на трафарете порошками разных цветов. В современном мире получили популярность необычайно красивые картины, выполненные этим методом, которые сегодня успешно украшают торжественные залы и дорогие рестораны.
Очень большой популярностью еще со времен Фаберже пользуются изделия, украшенные технологией гильоше с покрытием из эмали. Гильош – это орнамент, выполненный в виде густой сетки волнообразных линий, которые особым образом переплетаются между собой, создавая рисунок. Узоры гильоше придают поверхности изделий особую красоту, которая, переливаясь в лучах света, смотрится очень дорого и изысканно. Известная во всем мире фирма Фаберже разработала свыше 200 вариантов гильоша и еще в XIX веке использовала более 150 оттенков цветов. Знаменитые пасхальные яйца Фаберже до сих пор поражают любопытствующих игрой цветов и совершенством деталей.
Интересным фактом является то, что технология гильоширования настолько сложна, что до сих пор используется как один из видов защиты некоторых денежных купюр
Отличия горячей эмали от холодной
Горячая эмаль более прочная и цена на неё выше, чем на холодную. В холодном эмалировании существует ещё одна техника - финифть. После её нанесения она расплывается разноцветными узорами, подобно бензину на воде. Получаются своеобразные цветные разводы.
Горячая заливка более ровная, потому что прочная. На холодной эмали встречаются неровности, так как её не полируют. Ещё горячая глазурь ярко блестит.
У холодных смесей также находятся достоинства. Они отличаются простотой, неприхотливостью, пластичностью. Для изготовления таких украшений не требуются специальные инструменты. Холодное эмалирование подходит для любых сплавов.
Эмаль на золоте и серебре
Потрясающие коллекции золотых и серебряных украшений с эмалью заставляют трепетать сердца самых искушённых ценителей прекрасного. Среди огромного выбора серёжек, колец, браслетов радует глаз гармония сочных оттенков, огранённые самоцветы. Классика в виде чёрного и белого также сегодня в тренде.
Серебряные кулоны, подвески с эмалью выглядят просто шедеврально. Кольца с покрытием выпускают массивные и утончённые. Они иногда инкрустируются камнями. Оригинальные комплекты с эмалью станут украшением для девушек любого возраста и статуса. Отлично смотрятся гладкие, ровные колечки по типу обручальных, на которых нанесён греческий узор.