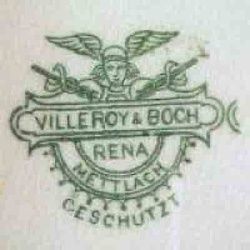
Villeroy & Boch - это три века мастерства и инноваций, это элегантнейшие произведения искусства и всегда стабильное качество, это одновременно художественные мастерские и высоко технологичное промышленное производство. Villeroy & Boch - это знаменитый бренд, известный во всем мире, прошедший за триста лет сквозь множество перипетий европейской истории, переживший кровопролитные войны на континенте и впитавший в себя лучшее, что было и есть в искусстве.
Это традиции, закаленные временем и постоянная работа над новым, во имя красоты и гуманизма. Никто не мог предположить такого успеха предприятия, когда в 1748 году основатель компании Франсуа Бох решил поменять профессию и заняться производством керамики. Франсуа Бох носил прозвище «Бомбардье-дю-Руа», поскольку был литейщиком королевских пушек.
Вместе со своими тремя сыновьями, он начинает производство керамической посуды. И это событие знаменует рождение компании Villeroy & Boch. Первая мануфактура была построена семьей Бох в Люксембурге в городе Сетфонтен в 20 километрах от столицы. Пьер-Иосиф, сын Франсуа Боха, подает заявку в правительство за разрешением и становится единственным среди многих, кто получает такое разрешение от императрицы Марии Терезии.
Императрица благоволит предприятию и дает высочайшее разрешение на название Manufacture Impériale et Royale. Именно тогда было начато производство популярной по сей день во всем мире посуды серии Старый Люксембург (Alt Luxemburg) с характерным орнаментом brindille (веточки). Эти орнаменты были разработаны Пьером-Иосифом Бохом в 1770 году. Сын Франсуа Боха Пьер был одаренным художником, с отличным чутьем предпринимателя, поэтому он сделал целый ряд художественных керамических изделий, и запустил их в серию. Некоторые из них сейчас можно увидеть в Музее Керамики Метлаха, например, распятие со змеей, или цветочные кашпо в стиле рококо. В 1797 году бизнесмен Николас Виллерой приобретает гончарную фабрику в Валлерфангене. Он вызывает специалистов из Англии и Франции для модернизации производства и становится одним из первых производителей керамики, использовавших уголь в качестве топлива для печей. Подвергается модернизации и технология декорирования керамики. Прежде всего, он начинает эксперименты с английской техникой трансфер-принтинга (печать рисунка на керамике), что существенно удешевляет производство. В то же время Жан-Франсуа Бох, второй сын родоначальника семейного предприятия Бохов, приобретает бывшее бенедиктинское аббатство в Метлахе на реке Саар. В здании в стиле барокко он устанавливает современные и широко механизированные системы производства посуды. Многие производственные машины он проектирует сам.
Его изобретения облегчили цикл производства и удешевили его. Фактически он привел свое предприятие к промышленному производству керамики. В то время, как второе поколение семьи Бох достигает оптимального качества продукции, экспериментируя с материалами, третье поколение делает решительный прорыв в технологии с Жаном-Франсуа Бохом - химиком, закончившим факультет точных наук Сорбонны. Жан-Франсуа разработал тип белоснежной керамики, очень похожей на фарфор, но значительно дешевле в производстве. Он открыл для своей компании практический способ демократизации фаянсовой посуды без утери ее качества и внешнего облика. На первой торговой выставке в Берлине в 1822 году предприятие получило золотую медаль, которая стала началом множества национальных и международных наград. Заводы Боха и Виллероя расположены не далеко друг от друга и обе компании весьма успешны на рынке. Но для того, чтобы развиваться дальше и удачно конкурировать, прежде всего, с английскими высоко-технологичными производствами, которые уже разорили не одно предприятие очевидно, что необходимо объединяться. Так родилась Villeroy & Boch — компания, сочетающая в себе сильные стороны обоих предприятий: творческий талант, предпринимательский дух, инновационный потенциал и производственные мощности. Компания стала одним из первых глобальных игроков XIX века.
Это объединение было в впоследствии закреплено и семейными узами: кланы поженили своих детей и племянников, а фирма стала переходить по наследству. Дети учились в самых лучших учебных заведениях Европы, а в 1892 году к фамилии Бох была добавлена дворянская приставка «фон». Семейство Виллерой-Бох дало миру также больших художников - Анну и Эжена Бох (пятое поколение семьи), известных импрессионистов и друзей Винсента Ван Гога, написавшего портрет Эжена, который сейчас висит в музее Орсэ в Париже. К середине XIX века Villeroy & Boch имела полный ассортимент продукции и поставляла крупные партии своей керамики в Париж, Варшаву, Лондон, Москву, Санкт-Петербург, Скандинавию, Италию, Испанию, Грецию, Турцию и Швейцарию. Около 1850 года были сделаны первые поставки керамики через Атлантику - в Северную и Южную Америку. А в конце XIX века Villeroy & Boch выбрали для участия в знаменитой Всемирной выставке в Лондоне. Лондон стал началом целой серии престижных выступлений на больших Всемирных выставках: в Филадельфии в 1876 году, в Париже в 1878 году и 1900 году, в Чикаго в 1893 году, в Санкт-Петербурге в 1901 году и в Сент-Луисе в 1904 году.
Среди интереснейших изобретений Villeroy & Boch в конце девятнадцатого века был фанолит (Phanolith) - полу-прозрачный фарфор, сочетающий в себе характеристики и преимущества яшмовой массы Веджвуда (jasperware) и технологию pâte-sur-pâte - пат-сюр-пат или paste on paste - метод украшения фарфора, в которых рельеф, накладывается с помощью кисти на необожженную, неглазурованную керамику последовательными слоями белого шликера. Создателем фанолита был художник-керамист Жан-Батист Шталь, возглавлявший секцию моделирования в Villeroy & Boch. Фанолит добился широкого признания на Всемирной Парижской выставке 1900 года, где Villeroy & Boch получили за него золотую медаль. Второе гениальное изобретение Villeroy & Boch - это так называемая, «метлахская плитка». Вообще, многие хорошие идеи можно найти в запасниках истории. Когда археологи наткнулись на римские мозаики в непосредственной близости от Метлаха, Евгений Антон Бох (четвертое поколение семьи) занялся их реставрацией. Под вдохновением этими археологическим находками, Евгений и его технологи начали экспериментировать с материалом для производства плитки. В итоге они разрабатывают производственный процесс, который позволяет производить плитку с феноменальной износостойкостью и сенсационно красивым внешним видом. С 1852 года в Метлахе начинается изготовление плитки по мотивам античных мозаик, которая известна теперь всему миру под названием Mettlacher Platten. Спрос на нее настолько велик, что в 1866 году компании приходится строить отдельный «мозаичный» завод, специализирующийся на производстве только этой плитки. А в 1879 году Villeroy & Boch приобретает керамический завод в Мерциге, на котором превращается в крупнейшего мирового производителя напольной плитки. Евгений Бох понимал, где именно будут расположены рынки завтрашнего дня. Поэтому построил еще один керамический завод в Дрездене, чтобы открыть новые экспортные возможности на севере и востоке Европы.
Производство первоначально было ориентировано на посуду, но довольно быстро переориентировалось на изразцовые печи и изразцовую плитку для облицовки стен. Наибольший вклад в репутацию дрезденского завода сделала облицовка изразцами магазинов, например, молочная Пфунда сегодня одна из самых популярных туристических достопримечательностей города, благодаря изумительной красоты изразцовой плитке с тонкой ренессансной росписью на стенах. Кафе в Музее Керамики в Метлахе является почти точной копией этого исторического магазина молочных продуктов. Не менее важным для компании направлением стало производство архитектурной керамики из терракоты. Под управлением Александра Шмидта ателье компании разработало уникальную глиняную смесь на основе терракоты для облицовки зданий. Причем, технологи ателье настолько улучшили материал, что по своим техническим характеристикам он превзошел даже камень. Достаточно сказать, что гигроскопичность метлахской плитки менее 0,3%, что позволяет использовать ее практически в любых климатических условиях. Терракотовые рельефы компании активно применялись в первую очередь для украшения зданий - соборов, банков, дворцов, богатых усадеб. Одним из таких зданий был, например, Замок Херренхимзее, где архитектурная керамика Villeroy & Boch не утратила своего первозданного вида до сих пор, хотя камень за эти годы уже покрылся бы мхом и частично разрушился. Villeroy & Boch создает мозаичный пол для Кельнского собора — здания, имеющего национальное символическое значение. Во время перестройки собора в XIX веке за пять лет компания создала и уложила более 1300 кв. метров мозаики.
В ателье Villeroy & Boch производится в промышленных масштабах посуда и черепица, создаются многочисленные предметы, сделанные специально на заказ. Компания становится поставщиком европейских правящих домов и высшего общества. Поставляется архитектурная керамика для всемирно известных престижных помещений: Большой театр в Москве или замок принца Турн-и-Таксис в Регенсбурге. Для коммерческих помещений - бассейнов, гостиниц, банков, и больниц и т.д. - с XIX века по наши дни было произведено огромное количество архитектурной керамики Villeroy & Boch. Производственные мощности в сочетании с художественными и техническими ноу-хау позволили компании разрабатывать и реализовывать выдающиеся индивидуальные проекты. В первой половине XX века Villeroy & Boch подхватывает движение Баухаус (Bauhaus) и элегантно роскошный стиль ар-деко, преобладающие в дизайне послевоенных двадцатых и тридцатых годов. Это также находит отражение в ассортименте компании. На рубеже века, Генри ван де Вельде - основатель Школы прикладных искусств (Kunstgewerbeschule), предтечи Bauhaus - создает дизайны для посуды и изразцовой плитки Villeroy & Boch. Баухаус – это художественная школа, основанная в 1919 году Вальтером Гропиусом. По своему типу и конструкции это было нечто совершенно новое в то время, поскольку в школе происходило слияние искусства и ремесла. Фактически Баухаус это первая и очень успешная попытка создания промышленного дизайна на основах классического искусства и архитектуры, их трансформации через призму авангардных течений и веяний. На сегодня Баухаус самое влиятельное учебное заведение в области архитектуры, искусства и дизайна. Баухаус считается школой авангарда и классического модернизма во всех областях изобразительного и прикладного искусства. Резонанс Баухауса продолжается и сегодня, как отражение образа модернистских течений. Компания Villeroy & Boch перестраивается. Сегодня это уже не просто производитель керамики, сегодня Villeroy & Boch – это поставщик образа жизни. Венделин фон Бох - представитель восьмого поколения семьи, продолжает стратегию расширения компании, делая ее интернациональной и наполняя новыми смыслами. Стоит сказать и о Метлахском музее компании Villeroy & Boch, который обладает обширной коллекцией керамики, насчитывающей более 17 тысяч предметов. Представляя в эффектных соотношениях традиции и новейшие разработки компании, экспозиция музея создает идеальные условия для ценнейших керамических экспонатов из последних пяти столетий, наглядно демонстрируя посетителям, что Villeroy & Boch удалось пронести стиль и элегантность сквозь века, развиваясь и держа высокую планку все триста лет своего существования.